Improving Quality Inspection of Flat Panel Displays with Imaging Colorimeters
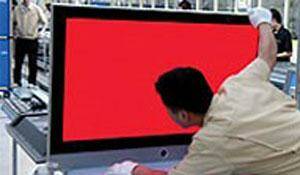
Perhaps no single component is as critical to the usability and perceived quality of today’s smartphones, tablets, and other electronics as their displays. Flat panel displays (FPDs) serve as the primary interface for these products; FPDs are also embedded in consumer products ranging from appliances, automobiles, and home security systems, to specialized commercial products for the medical, industrial, and defense industries. The importance of display quality to the success of these products and the cost – in both customer experience and the direct cost of repair and replacement - of shipping flawed products is driving manufacturers to seek alternatives to today’s quality control tests that rely on human inspection.
Human inspectors provide the benefit of human vision - that is to say that they see variations in brightness and color and notice defects in the same way the end user will – but lack the repeatability and speed of an automated system. Human inspectors can also miss subtle variations in light and color (mura) that are difficult to perceive during the abbreviated factory inspection process, but will be visible to an end user viewing the display for an extended time period.
What is needed is an automated, objective means of replicating human visual perception that does a better job of reflecting real end customer perceptions and experience. This capability is provided by imaging colorimeters, which are specialized image-based measurement systems that are calibrated to have the same response to light, brightness, and color as standard human vision, as defined by CIE (International Commission on Illumination) models. Paired with analytical software designed for high volume manufacturing, they detect defects and assess contrast, brightness, and color uniformity in FPDs. Imaging colorimeters can be used in a fully-automated testing system, bringing speed, repeatability, and flexibility to the inspection process, combined with the relevance and accuracy of human visual perception.
Challenges in Flat Panel Display Inspection
Effective measurement and analysis in a production environment depends on meeting three objectives during the testing process:
(1) identify defects with a high correlation to human visual perception
(2) quantify the severity of the defects
(3) perform analysis rapidly and with high repeatability
A fundamental difference between imaging colorimetry and traditional machine vision is imaging colorimetry’s accuracy in matching human visual perception for light and color uniformity (and non-uniformity). This makes it ideal for identifying (1) and quantifying (2) defects to assess visual performance of FPDs. The analysis and quantification of defects can be used to determine next actions, such as whether to scrap the device / display or to repair it.
Imaging colorimeters provide testing speed and repeatability that human inspection cannot match. By specifying an appropriate automated test sequence, an imaging colorimeter can be used to obtain extensive, accurate, high-resolution data to describe the performance of a particular display. This measurement data can often be obtained, depending on the display technology and resolution, in a few seconds to a minute for typical test sequences.
System Configuration
Automated measurement and analysis of displays with an imaging colorimeter requires combination measurement control and analysis software. The key components of the system are:
(1) a scientific-grade imaging colorimetry system;
(2) PC-based measurement control software which both controls the imaging colorimeter and test image display on the device under test; and
(3) a suite of image analysis functions that allow various tests to be run.
The result is a system that can deliver quantitative, automated inspection for a variety display defects, such as point defects, line defects, and mura.
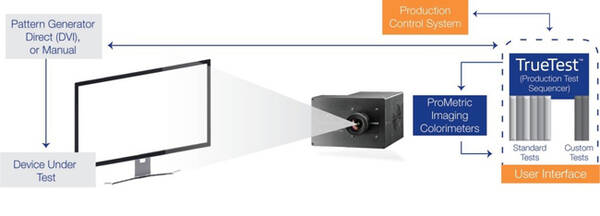
FPD Inspection Applications
Capturing images of an appropriate series of test patterns, ranging from simple uniform white, grey, or black screens to color screens to defined geometric patterns, provide the input to automated inspection analyses. The exact images to be captured will be dictated by the requirements of a given application; this will be a function of where in the production process the tests are being performed – outgoing quality control, incoming quality control, or inline testing. Imaging colorimeters can replace human inspection of assembled displays, display panels, touch panels, back light units, and other sub-assemblies. Tests can be generalized into a few categories:
- Display quality: Tests such as brightness and color uniformity, chromaticity, and contrast for BLUs, display panels, and assembled displays. Generally these performance parameters are represented by absolute measurements. For example, a luminance value must fall in a specified range. The ability to collect objective data represents a huge advantage over human inspection, ensuring consistency when evaluating multiple FPDs.
- Defect detection: Some defects have well defined physical characteristics, such as point defects and line defects. Others are more random in structure, such as light leakage and mura. Defects may be LCD based, or can be associated with other FPD sub-components, such as polarizers. For mura, both detection and classification can be complex First, because the mura area can vary in size and shape and, second, because a human’s ability to perceive the mura is a function of additional attributes – viewing distance, spatial frequency, and color.
- Detection of foreign material: Dirt, smudges, fibers, or other foreign matter can be detected with an imaging colorimetry system. Typically this is done prior to a manufacturing step that would lock these in as defects and often requires both display illumination and external surface illumination to distinguish embedded artifacts from surface artifacts. Unlike human inspection, the system can be used to find and size significant small defects virtually instantaneously.
Conclusion
FPD inspection with imaging colorimeters can be applied to multiple display technologies including LCD, plasma, and OLED. By providing rapid, repeatable measurements that are correlated to human visual perception and by being able to numerically characterize them, these methods allow display defects to not only be identified, but also classified by cause. This allows a consistent measurement of displays in manufacturing applications, providing an automated determination of pass / fail in accordance with user defined criteria and objective data from which to base remedial actions.
Join Mailing List
Stay up to date on our latest products, blog content, and events.
Join our Mailing List