Raise a Glass to Glass
Many of us (about 50% of s
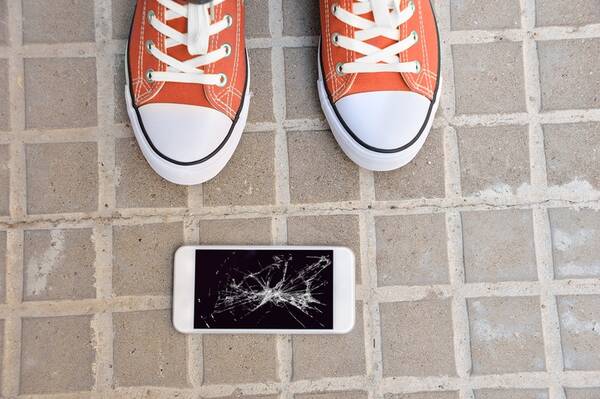
Evolution of Glass
Historians estimate that glass was first produced in Mesopotamia in 4000 B.C. It’s been called one the most important materials in human history.2 From stained glass windows in Medieval cathedrals, to eyeglasses, tempered glass automobile windshields, and the fiber-optic cables that connect today’s global communications networks, glass is all around us. More than 7 billion3 of us carry glass in our purses and pockets every day in the form of cell phone screens. Even with today’s tougher cover glass, mobile phones and devices are still vulnerable to scratches and cracks.
Protective cases and stick-on layers can help mitigate potential damage, but the pursuit of durable and damage-resistant glass is a continuing push in the industry, with the twin (although sometimes opposing) objectives of scratch resistance and shatter resistance. Modern glass manufacturers have already “shattered” the myth that glass is fragile. Some innovations in this area include:
- In 2012 Corning, Inc.* released Gorilla Glass®, a toughened transparent glass material composed of an oxide of silicon and aluminum (aluminosilicate) that is immersed in a proprietary hot potassium and sodium ion bath. It is thin, light, and damage resistant—just the qualities smart phone and mobile device makers need. While there are other, similar products available, today roughly 5 billion devices worldwide use Gorilla Glass. (If you want to learn more about the chemical structures and properties of smart phone glass, the American Chemical Society provides a detailed overview.)
- Sapphire glass is a synthetically produced version of the sapphire gemstone. It’s very hard (rated 9 on the Mohr hardness scale; diamonds are rated 10), making it extremely rugged and durable. However, it’s expensive and energy-intensive to produce. It is highly transparent over a broad spectrum of light including the visible spectrum (~350-750 nm), and scratch-resistant. However, it’s somewhat brittle, thus prone to cracks from a drop impact. Today it’s used most commonly in retail bar-scanners, as watch crystals, as an electronic wafer substrate, and in some smart phone devices for camera lenses.
- The latest generation of Gorilla Glass (5) has been developed to fully withstand a drop from the height of 1.8 meters, aka “selfie height” (the typical height at which people hold out their phones to take a selfie), at least 80% of the time.
- Taking a look at future glass developments in pursuit of “unbreakable” smart phone screens, various companies are currently working on ideas like synthetic diamond glass and ultra-thin flexible glass ribbons. Researchers in both the US and Japan have even come up with “self-healing” glass and polymer materials that can be molded back together to fix a crack.
Flexible Glass Devices On Display
Along with the previous requirements of scratch resistance and shatter resistance, there is now a new objective for smart phone screen covers: flexibility. Foldable, roll-able, and stretchable displays were a hot topic at this year’s SID Display Week. For example, Chinese display maker BOE exhibited flexible OLED displays, including a paper-thin display that fluttered in the breeze:
Samsung demonstrated its 14” rollable active-matrix OLED (AMOLED) display:
And Corning, Inc. was there touting this as The Glass Age. The company’s Director of Business Technology, Millicent Ruffin, even showed off a glass version of the Slinky®, as flexible and springy as its metal namesake!
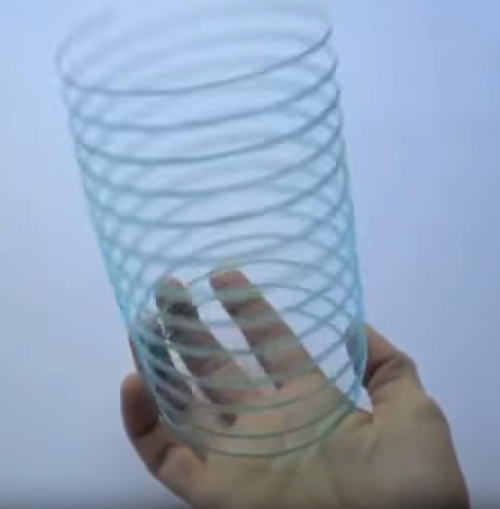
However, conference speaker Mike Hack of Universal Display Corporation made the point that when people talk about flexible phones today, they (with or without knowing it) are usually talking about devices with plastic screen covers, not (yet) glass. The challenge is that the cover film (whether glass or other material) for a foldable display must provide:
- Glass-like high strength
- Plastic-like low modulus
- Rubber-like elasticity (elongation)
- Optical transparency
A mix of hardness and foldability with dynamic/static reliability is hard to achieve. For a flexible OLED panel, for example, an ideal glass substrate must have:
- Low total pitch variation (up to 45% better than alternative display glass)
- Low total thickness variation (up to 2x better than alternative display glass)
- High UV transmission (ensuring less hazardous blue light and less eye strain)
As the display industry evolves towards using more OLED, AMOLED (particularly in smart phones), and microLED displays, these glass requirements are coming to the forefront. With the growth of AR/VR technology, the demand for high-performance yet very thin and light glass for wearable displays is also growing.
Ensuring Glass and Screen Quality
Whatever type of glass or screen cover is used on a phone or other display device, durability isn’t the only challenge manufacturers face—making sure the material itself is free of defects such as particles or surface scratches is just as important. Customers of today’s high-quality smart phones expect them to start out perfect and stay perfect.
The manufacturing process for glass is extremely precise. Defects can include air bubbles, stretching, particles, and unevenness. To combat this, for example, Corning has developed an advanced fusion production method used to maximize the quality and consistency of Gorilla Glass and other products.
Beyond controlling the purity and consistency of the glass itself, display device manufacturers are also tasked to minimize defects during the process of assembling all display layers—from to the base LCD to the touch layer, cover glass, and any anti-glare or other applied films. At every step there is the potential to introduce particles, blemishes or smudges on the surface (e.g., a fingerprint), or cause other damage (dings and scratches).
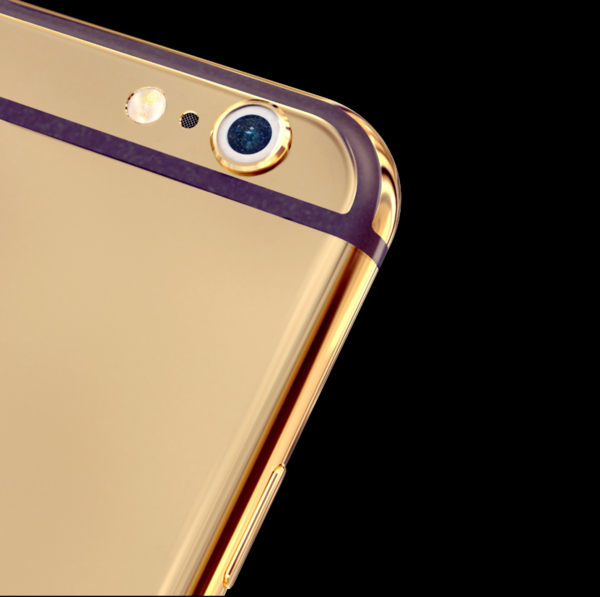
Dust under this smart phone camera lens may result in costly rework or a returned product.
Radiant’s ProMetric® imaging photometers and colorimeters provide the high-resolution, precision visual inspection necessary to spot, quantify, and correct many issues in display quality. Imaging colorimeters provide early identification of defects, reducing overall production costs by preventing additional investments from being made into flawed assemblies. Detection of foreign material, including dirt or fibers, can be performed at key points in the manufacturing process to avoid locking in these defects under film or glass.
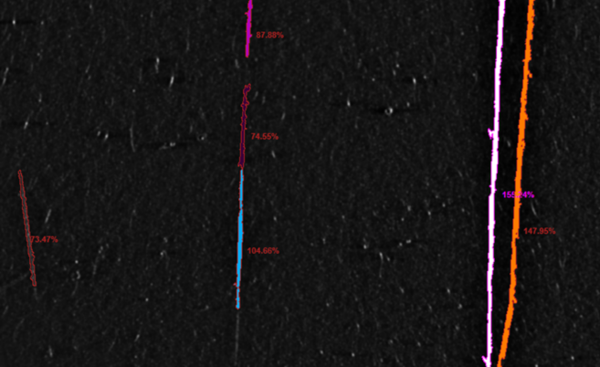
Scratch analysis image.
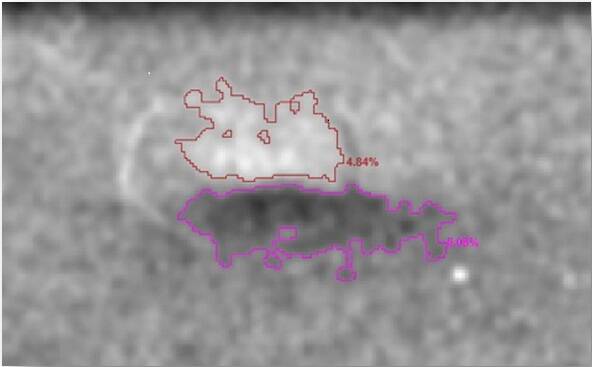
Dent analysis image.
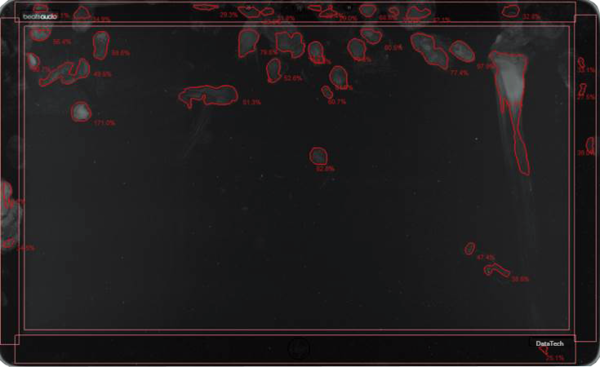
Smudge analysis image.
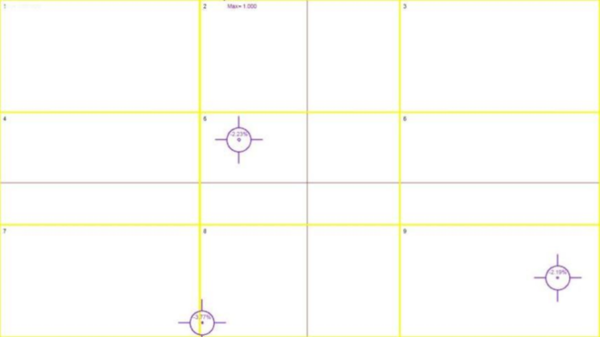
Particle analysis image.
Unlike human inspectors, an automated surface inspection system from Radiant can find and measure significant small defects in displays instantaneously and repeatably. It can zero in on defects regardless of their location; for example, identifying whether a smudge or particle is located on the top or bottom of a transparent layer—can it be wiped off, or does the unit have to be discarded?
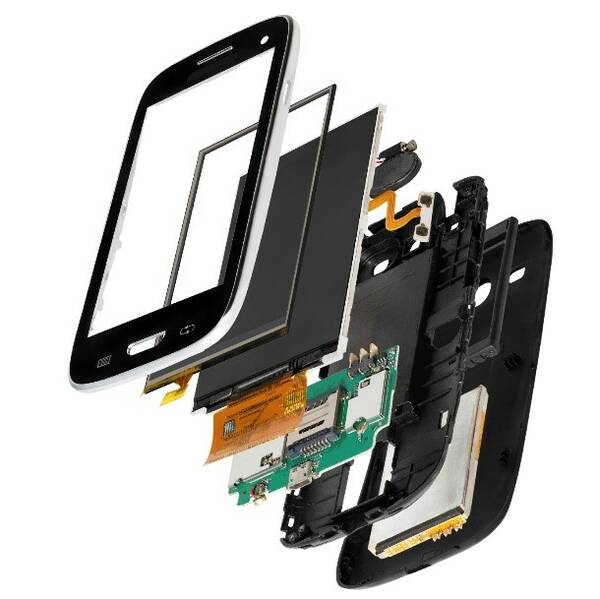
Developers and inventors are working on the next generation of glass and other materials that can provide the flexibility, durability, thinness, and performance demanded by future display devices. And Radiant is working alongside them to provide the most precise and efficient measurement to ensure the finish quality of those displays.
--------------------------
1. Nazarian, Robert, “How bad is the cracked cellphone screen epidemic? Motorola gives us the lowdown.” on Digital Trends, October 30, 2015. https://www.digitaltrends.com/mobile/motorola-shattershield-cracked-sma…
2. Main, Douglas, “Humankind’s most important material." The Atlantic, April 7, 2018. https://www.theatlantic.com/technology/archive/2018/04/humankinds-most-…
3. Boren, Zachary D., "There are officially more mobile devices than people in the world." Independent, October 7, 2014. https://www.independent.co.uk/life-style/gadgets-and-tech/news/there-ar…
*The author has no direct relationship to Corning, Inc. This blog post is not intended to be an endorsement by the author or by Radiant Vision Systems of any third-party product, nor have we received any payment or consideration to feature any company’s products here. In the interest of full disclosure, the company of Corning, Inc., was named for the town of Corning, NY after locating its headquarters there in 1868. Corning, NY had been named after Anne Corning’s ancestor, Erastus Corning, a 19th-century mayor of Albany, financier, and railroad executive.
Join Mailing List
Stay up to date on our latest products, blog content, and events.
Join our Mailing List