Fun with Flexible Displays & Form Factors: A Display Week Review
Displays are breaking out of their flat rectangular box! Last week at the 2019 SID Display Week exhibition we saw a television screen that rolls down into a box, many foldable phones, cylindrical screens, a sculptural OLED “rose”, a mini-display wrapped around a lamp—even a flexible OLED Chinese opera mask. All of these examples were designed to highlight the flexible application of emerging emissive displays.
Tianma’s Chinese opera mask uses a flexible OLED display. Video credit: Dave Haynes, sixteen-nine.net.
The display industry gathered in San Jose, CA, last week to see the latest technology innovations for televisions, smartphones, tablets, automotive consoles, and displays of all types. A few curved and flexible panels were a novel addition at 2018 Display Week, but this year it seemed like form factor innovation was everywhere. Flexible displays even took center stage for the first time with the inclusion of a new SID/DSCC Foldable Display Market Focus Conference.
Flexible Displays on Display
A few standouts from the show floor are spotlighted below.
This 65” rollable OLED television from LG Display rises from a low console, up to full height, then rolls back out of sight:
This foldable phone from Tianma (below) was just one of the many small-screen flexible and foldable displays at the show:
“The Rose” was sculpted by LG Display out of 4 curved OLED display panels (first shown at CES 2019) that continuously “bloomed” with completely synchronized designs and images:
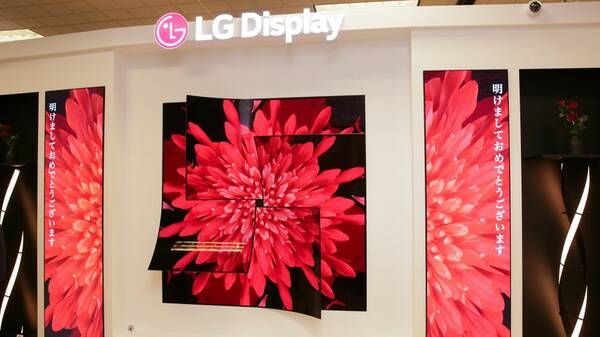
Photo credit: OLED-Inside
Visionox showed a host of unique form factors and display devices at their booth:
Video credit: Dave Haynes, sixteen-nine.net
OLED Makes Flexibility Possible
The innovation that is enabling all of these latest creative shapes is Organic Light Emitting Diode (OLED) technology. OLED displays are emissive and do not require a backlight, thus they are thinner, bendable, and better suited for different form factors. In addition, they are more energy efficient than LCD displays. The main component in an OLED display is the OLED emitter—an organic (carbon-based) material that emits light when electricity is applied. The basic structure of an OLED panel is an emissive layer sandwiched between a substrate (backplane) and an encapsulation layer (typically thin film encapsulation, or TFE).
OLED elements can be deposited onto glass substrates for rigid flat-panel displays, or onto other types of substrates. The flexible smartphone models and wearables released thus far on the market have been AMOLED (active-matrix OLED) layers placed on plastic (polyimide) substrates.
Still Some Challenges
There is a lot of excitement surrounding flexible device innovation, but despite the many shown during Display Week, these products still have barely reached the consumer market. Early this year, Samsung and Huawei were both poised to release foldable phones, but both have hit bumps in the road. Samsung’s much-anticipated Galaxy Fold was delayed due to defects in the screens, and is now only available for pre-order. Meanwhile, the Huawei Mate X faces questionable support prospects from Android following a recent White House executive order banning sales of Huawei’s products in the U.S.
Additionally, market factors like cost and price come into play, along with potential competition from emerging microLED and quantum dot displays. Even the prospect of a continuing trade war between the U.S. and China poses a barrier that could slow the mass market success of OLED devices. Nevertheless, OLED manufacturers continue to work on various challenges in OLED fabrication and assembly, production yields, and durability to match growing customer demand. These challenges include:
- Material lifetime and potential “burn in” (residual images on the screen after the display projection changes)
- Efficiency (especially of the blue OLED material)
- Soluble OLED material performance and production processes
- Flexible OLED encapsulation
- Better backplane materials for flexible and foldable OLEDs
- Scaling evaporation processes for direct-emission OLEDs beyond Gen-6 fabrication
Meeting OLED Quality Demands
Radiant can help resolve product quality issues before devices reach the market. Inspection of LCD flat panel displays is a well-established discipline and Radiant has hundreds of cameras inspecting millions of these displays worldwide. However, emissive displays like OLED, microLED, and QLED require more advanced inspection solutions capable of discerning pixel and sub-pixel level detail with high precision.
Unlike LCD displays lit by a single LED backplane subject to only moderate variation, each individual emitter in an OLED display can exhibit a great deal of variation from pixel to pixel. This variability makes inspecting for defects and uniformity more difficult and requires a visual inspection solution capable of both high-resolution data capture and image quality.
Radiant’s ProMetric® Imaging Photometers and Colorimeters—including our latest Y-Series 43-megapixel imager—strike the balance between capturing high-resolution images while minimizing noise and providing high dynamic range for the most accurate measurement of tiny light-emitting elements. Combined with our TrueTest™ software, Radiant solutions are helping OLED device manufacturers to identify defects (such as dead pixels) and non-uniformity (mura) to ensure a perfect viewing experience for all display customers.

Join Mailing List
Stay up to date on our latest products, blog content, and events.
Join our Mailing List