Radiant at 30 – Staff Stories: Product Evolution Never Stops
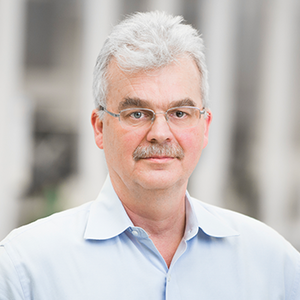
Jens Jensen is Radiant’s Vice President of Product Development. He joined the company in 2010.
Before I came to Radiant, I worked for a Danish company: a large test house that had production of optical filters, instrumentation for road marking, and notably, also made colorimetric camera systems. I had known Ron [Rykowski, co-founder of Radiant] for many years through international standardization work and I met Doug [Kreysar, then-COO of Radiant] at a conference.
I started as a Staff Software Engineer, but with 23 years of experience in photometry, colorimetry, and measurement, including camera systems, I brought technology knowledge too. Radiant had about 30 people—it felt like a mom-and-pop shop to me. My previous company had 350 people doing testing for the air force, the navy, and many entities that had to abide by regulations.
I was the technical lead of the accredited photometric and colorimetric laboratory. When I started at Radiant, we had one room where the cameras were assembled and a dark room for some calibrations, but it was certainly not an optical lab like I was used to. Our current cleanrooms in Redmond and Suzhou and our software-controlled calibration stations are certainly a big step up from 12 years ago!
When 3D Movies Were All the Rage
We once went into development of 3D display measurement—this was at a peak of excitement for 3D displays—looking at the view for the left eye and right eye. But 3D died out once again and you don’t see it much anymore except as a novelty. We had the F-series ProMetric® camera and wanted to modernize it. As the development of the new model progressed, I took the lead, working with the mechanical design and electronic engineers. Much development effort went into reducing stray light to enhance image contrast.
To build the G-series camera, we put a new wrapping of molded plastic housing components over some existing technology. As a major development, we introduced an electronic lens with automated calibration stations. Not long after, high-quality interline sensors came on the market, and we added a larger sensor to the camera. We had to do a lot of development on the electronics for that, and also had to update the software so it could chew on a much larger amount of data (up to 16MP per color channel at the time).
Next, we started development on the 16MP Y-Series ProMetric® camera for photopic or radiometric measurement. The Y-series cameras were also developed with the electronic lens, and we designed a new extruded aluminum housing that was more efficient to produce and maintained rigidity with a lot less housing material.
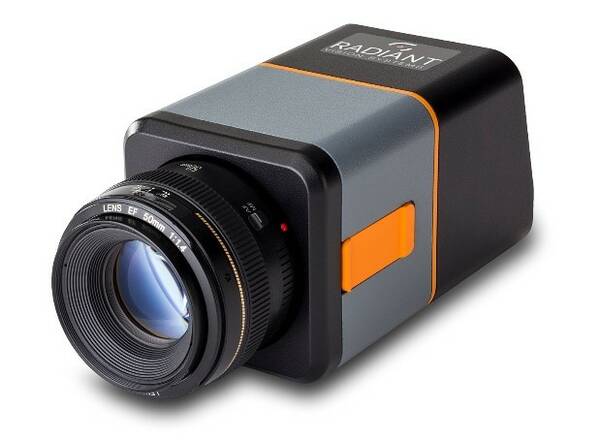
Radiant’s ProMetric® Y-Series Imaging Photometer, still the workhorse of many lighting and display measurement applications.
From the Lab to the Line
Our filter wheel mechanics consisted of six or eight plates, many spacers and about 50 screws. With our I-series colorimeter, we introduced a molded filter wheel which was a big improvement for the production process. It was also lighter so the color measurements could run faster.
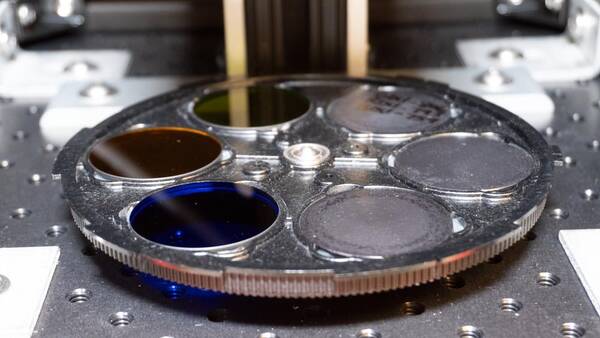
One of Radiant's molded filter wheels.
As our customer base evolved from lab users to production lines, speed became more and more important. Interline sensors were faster than the old full-frame sensors in the F-Series and G-series. From a measurement time of around 20 seconds, we brought it down to just one second or half a second in the new cameras. They could also take an image with 3-4 times more pixels—improving both speed and resolution.
Sensor & Optics Evolution
We are never making just one change to our cameras because each new element—filters, sensors, extrusion technology—necessitates associated updates, and the software must keep up. We’ve expanded our team on the optics and mechanical side and added more programmers.
Most recently, we’ve done new development to incorporate larger CCD and CMOS sensors like 45MP, and 61MP. When onsemi phased out its CCDs we had to adapt quickly. We did a lot of testing to ensure the latest CMOS sensors could meet or exceed the high-quality imaging of our previous systems.
One focus in the last several years has been the optics—we have a whole department for that now. We’ve added conoscopes and developed near-infrared (NIR) measurement systems. Measuring AR/VR devices also required new optics. We’ve enhanced optical quality for customers who need to measure display pixels, introducing a microscope lens to look for details within individual pixels.
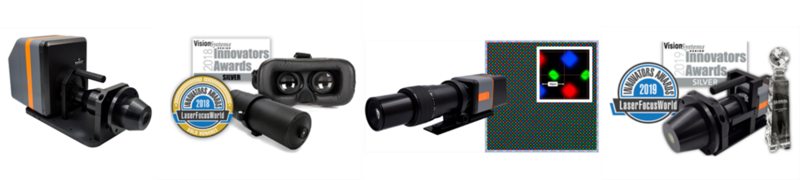
Radiant now offers specialty lenses with a range of optical properties to serve different application needs. From left to right: FPD Conoscope Lens, award-winning AR/VR Lens, Microscope Lens, award-winning NIR Intensity Lens.
Always Moving Forward
In product development, we are always looking at where the market is trending—measuring different wavelengths, new optical configurations, new display technologies—but most importantly, we listen to customers to understand what they need. For example, alignment between the camera and device under test now must be more precise, down to a few microns. We’ve done a lot of mechanical development there; we’ve changed the sensor technology, the filters, the quality of the optics. We’ve introduced new mechanics in the housing and new alignment mechanics for a lot of our products.
With higher- and higher-resolution camera systems we also need to upgrade computing power and continually upgrade the software. It’s an ongoing process, always adapting to new technologies and enhancing our systems to improve capabilities, quality, and speed.
To respond to customer requests and any surprises the market throws at us, we must stay nimble. I have never seen a year turn out as we had expected and planned for. Agility from everyone is an important factor in Radiant’s success.
Join Mailing List
Stay up to date on our latest products, blog content, and events.
Join our Mailing List