Today's 3D Sensing Applications Depend on VCSEL Performance and Accuracy
The first laser device was built in 1960 by Theodor Maiman at Hughes Research Laboratories in Malibu, CA, from a cylinder of synthetic rubber and photographic flash lamps.1 The concept had been described by Albert Einstein back in 1917 with his theory of stimulated emission, but it took decades and the development of microwave spectroscopy in the 1950s before a detailed proof of concept could be created by Charles Townes and Arthur Schawlow.2 Their 1958 paper led to a patent for the “light amplification by stimulated emission of radiation” device, or laser.
A characteristic of laser light is that it is coherent, meaning the wavelengths emitted by a laser diode are all in phase in space and time. This makes lasers typically monochromatic and quite powerful, but also more hazardous as they can deposit a large amount of energy on a very small area. Today lasers are ubiquitous in the marketplace and in our daily lives, used for everything from fiber-optic communications to corrective eye surgery to supermarket scanners.
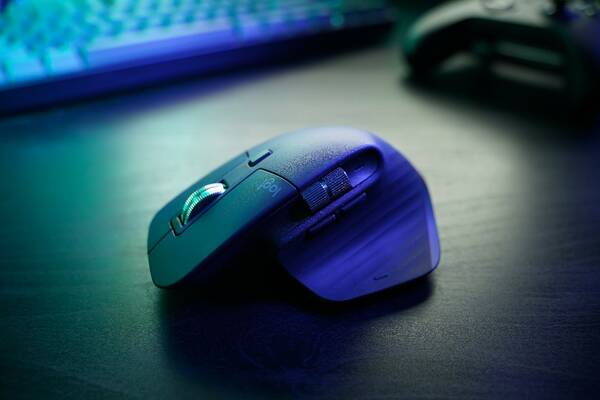
The Logitech MX3 is one of the latest models of computer mice that use near-infrared laser sensing for operation.
Vertical-Cavity Surface-Emitting Lasers (VCSELs)
In 1977, Kenichi Iga created the first vertical-cavity surface-emitting laser, or VCSEL. The technology was further developed over the next decade-plus at Bell Labs by Jack Jewell and others. VCSELs have since become ubiquitous in many industrial, commercial, and consumer device applications, particularly for 3D sensing that relies on near-infrared (NIR) light.
VSCELs are composed of layers of semiconductor materials grown on an epitaxial substrate as individual wafers. Each VCSEL diode generates light between two layers of Bragg mirrors (distributed Bragg reflectors, or DBRs) that are parallel to the surface of the wafer, forming a cavity, or resonator region, with several quantum wells. This monolithic laser resonator radiates the light vertically to the surface of the semiconductor chip, as opposed to edge-emitting laser diodes (EEL), where the light exits at the edge of the chip. Although this vertical emission architecture can result in a lower power light, the beam quality of VCSELs is typically higher than that of EELs—or of LEDs, which are also used for NIR sensing applications—a trade-off for better performance and reliability.
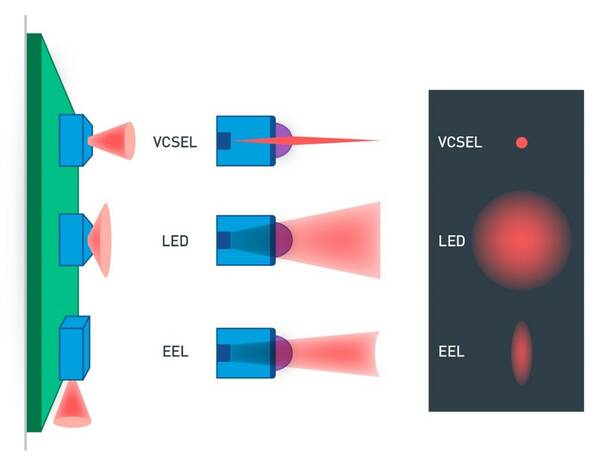
Comparison of VCSEL, EEL, and LED light sources in terms of beam direction and spatial light distribution. (Image: Source)
There are multiple benefits of the vertical design: “VCSELs offer coherent light with direct emission, high power density, and simple packaging. The VCSEL structure is easier to assemble than a comparable EEL…Compared with edge emitters, VCSELs’ simple beam structure considerably reduces the complexity and cost of the coupling/beam-shaping optics and increases the efficiency.”3
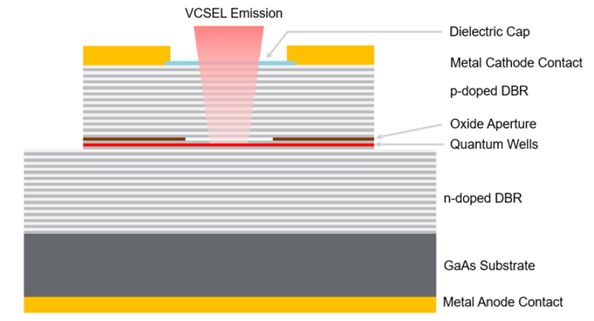
Structure of a typical VCSEL: two distributed Bragg reflector (DBR) layers with quantum wells in between, emitting light from the top of the unit. (Image: Osram)
VCSELS can be used in many different ways, with some of the most common applications in the realms of precision sensing and high-speed communications. In fact, VCSELs have found a place in “3D sensing, lidar, automated driving and manufacturing, high-speed data communication, laser printers, optical mice, and smartphones,”4 along with applications in biomedical and gas sensing, and computing. This versatility is driving a boom in the VCSEL market, which is projected to nearly triple in size from revenues of $1.1 billion in 2020 to $2.9 billion by 2025 (a CAGR of 23.7% over the time period)5 and to surpass $5 billion by 2027.6
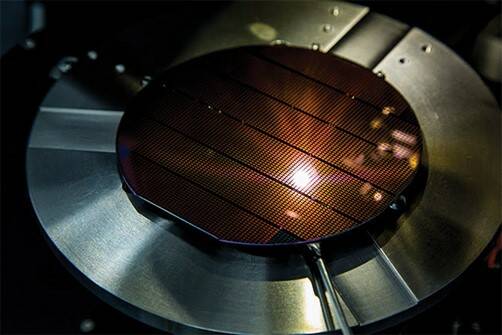
A VCSEL wafer in production. (Image: Photonics Media)
VCSEL 3D Sensing Applications
VCSEL-based sensing has become widespread for facial and gesture recognition, eye tracking and iris detection, lidar and autonomous vehicle sensing, driver monitoring and occupant monitoring systems (DMS and OMS), and multi-modal sensing for gesture and motion control. One reason VCSELs have become the technology of choice for 3D sensing is their use for time-of-flight (ToF) measurement. ToF sends out a beam of NIR light, measuring the time gap between when the signal is emitted from a source (such as VCSEL or LED) to when the signal returns after being reflected off an object.
The return signal is captured by an NIR camera. The time difference from emission and return is the signal’s “flight”, which indicates the distance of the object. This depth measurement enables 3D measurement of objects such as a human face (for facial recognition applications) or an obstruction in the road (for automotive lidar).
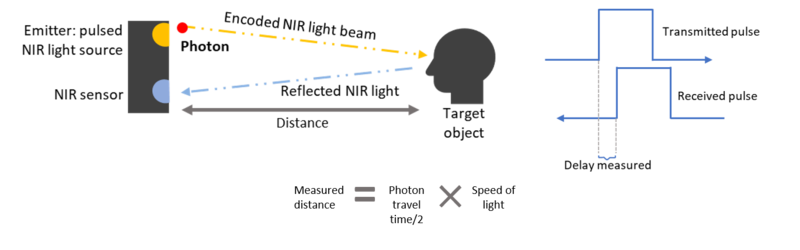
Representation of Time-of-Flight measurement using a near-infrared emitter such as a VCSEL.
In ToF applications, VCSELs offer the benefits of “fast scanning, long operating distances, high efficiency, and excellent resistance to ambient-light interference. In 3D depth detection modules, VCSELs enable wavelength, brightness, size, and beam-angle selection to suit the application.”7
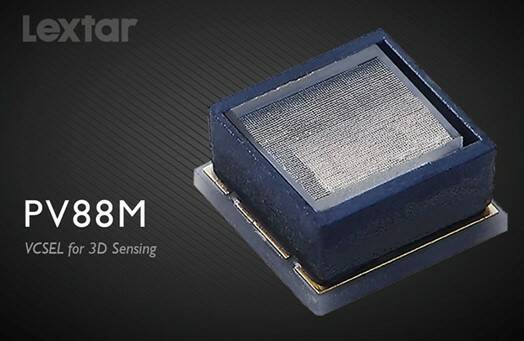
The VCSEL PV88m from Lextar, which is used for 3D depth detection, tunable for the appropriate wavelength, brightness, dimension and beam angle from 45°-100°. (Image © Lextar)
The Need to Measure VCSEL Emitters for Accuracy and Safety
For 3D sensing applications, VSCELs from 810 nm - 940 nm are typically used. However, these NIR wavelengths are invisible to the human eye, with the potential to cause damage from exposure over time. Thus, special care is required to ensure the laser’s emissions are within the intended performance parameters.
For manufacturers of VCSEL-based devices, test equipment must be used during production to ensure accurate intensity and distribution of NIR light. Radiant offers an NIR measurement solution specially designed for use in the lab and on the production line to ensure consistency and quality of these emitters.
VSCEL Measurement Solution
The Radiant Vision Systems Near-Infrared (NIR) Intensity Lens system is an integrated camera/lens solution that measures the angular distribution and radiant intensity NIR emitters, both VCSELs and LEDs. The system uses Fourier optics to capture a full cone of data in a single measurement to ±70 degrees, providing extremely fast, accurate results ideal for in-line quality control.
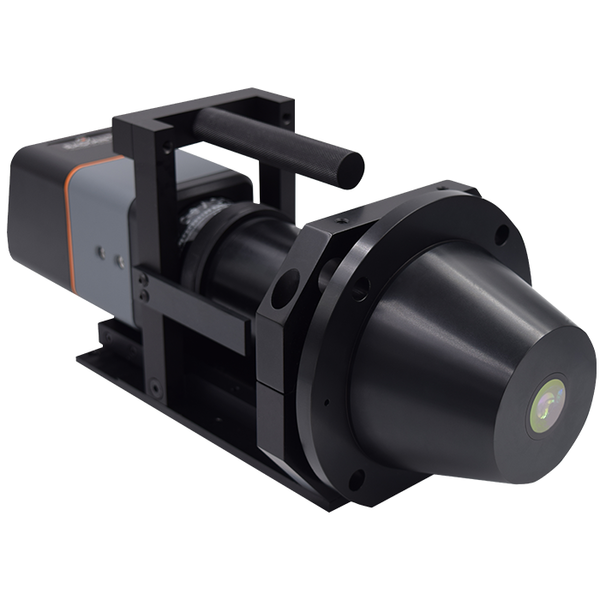
Radiant’s solution for NIR VCSEL and LED measurement: the NIR Intensity Lens integrated with a ProMetric® Y-16 Radiometer.
Manufacturers of 3D sensing technology can apply the NIR Intensity Lens solution for direct angular measurement of NIR LEDs, lasers, and structured light patterns produced by Diffractive Optical Elements (DOE). The lens mounts to a Radiant Vision Systems ProMetric® Y16 Imaging Radiometer, and features ProMetric or TrueTest™ Software for intuitive system setup and customizable automated measurement sequences.
Additional tests specific to NIR emission measurement are available in the TT-NIRI™ Software test suite. Users can sequence tests for rapid evaluation of all relevant display characteristics in a matter of seconds, applying multiple selected tests to a single image captured by the camera. Unique tests for NIR analysis include:
|
|
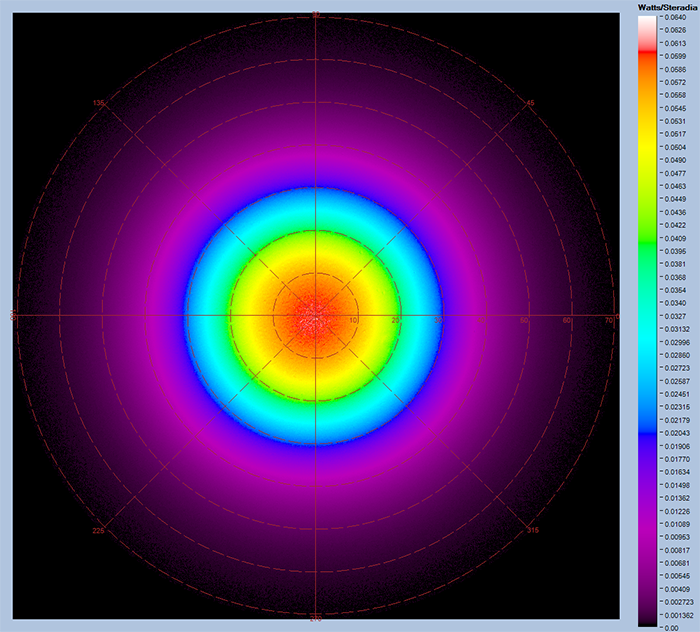
The angular distribution of an NIR emitter, as captured in a single image by the NIR Intensity Lens and shown in false color (heat map) polar plot generated in TT-NIRI analysis software.
Applications such as eye tracking, facial recognition, and automotive lidar that are used on and around humans require rigorous testing to comply with industry standards. Radiant’s measurement solutions characterize the output of NIR sources, providing manufacturers with data that may be useful when testing to these standards.
The new generations of devices that use NIR laser emitters for 3D sensing demand new approaches to product quality testing to ensure performance and accuracy. The Radiant NIR Intensity Lens solution offers the advantage of speed, size, and software for precise measurement of 3D sensing systems.
CITATIONS
- “A History of the VCSEL”, Photonics Media, May 18, 2020.
- “This Month in Physics History: December 1958: Invention of the Laser”, American Physical Society (APS) News, Vol. 12, No.11, December 2003.
- Emilio, M., “Vertical-Cavity Surface-Emitting Lasers Hit the Target for Depth Detection,” EETimes Europe, January 1, 2020.
- Ahmed, F., “Low-Powered VCSELs Find a Wide Variety of Uses, Photonics Spectra, December, 2018.
- “VCSEL Market by Type (Single-mode, Multimode), Material….and Geography – Forecast to 2025”, Markets and Markets Report, April 2020.
- Wadhwani, P., and Yadav, S., “VCSEL Market Size Worth Over $5bn by 2027,” Global Market Insights, February 1, 2021.
- Emilio, M., “Vertical-Cavity Surface-Emitting Lasers Hit the Target for Depth Detection,” EETimes Europe, January 1, 2020.
Join Mailing List
Stay up to date on our latest products, blog content, and events.
Join our Mailing List