Turning Up the Heat: Display Device Performance & Durability on a Warming Planet
As the impacts of global climate change are being felt around the globe, humans are bracing themselves for more extreme weather events such as “heat domes”, storms, and drought. Locations from Alaska to Australia, Siberia to South Africa have been experiencing record-setting high temperatures in 2020-2021.
Rugged displays are a standard feature in the aviation, automotive, and maritime industries, and in the military, where exposure to a harsh ambient environment can be a regular part of operation. Rugged displays are built to continue functioning at temperatures ranging from -20°C (-4°F) to 50°C or even as high as 70°C (158°F).
To ensure temperature resilience, these devices differ from standard, consumer-grade display devices in multiple ways. For example, they use solid-state hard drives without moving parts and chemically treated display cover glass for increased resistance to cracks and breakage. They also typically rely on backlight displays for the most consistent readability in all ambient light conditions. For displays on planes flying over the arctic in frigid weather or ships sailing across the equator under the glare of tropical sunlight, these extra design parameters and specialized materials are cost-effective and necessary for operation and safety.
With the specter of global warming, however, even standard displays such as home televisions, personal laptops, and smartphones are at increasing risk of exposure to more extreme temperatures. Billions of households and millions of workplaces around the globe do not have air conditioning, leaving electronics devices at the mercy of the ambient environment.
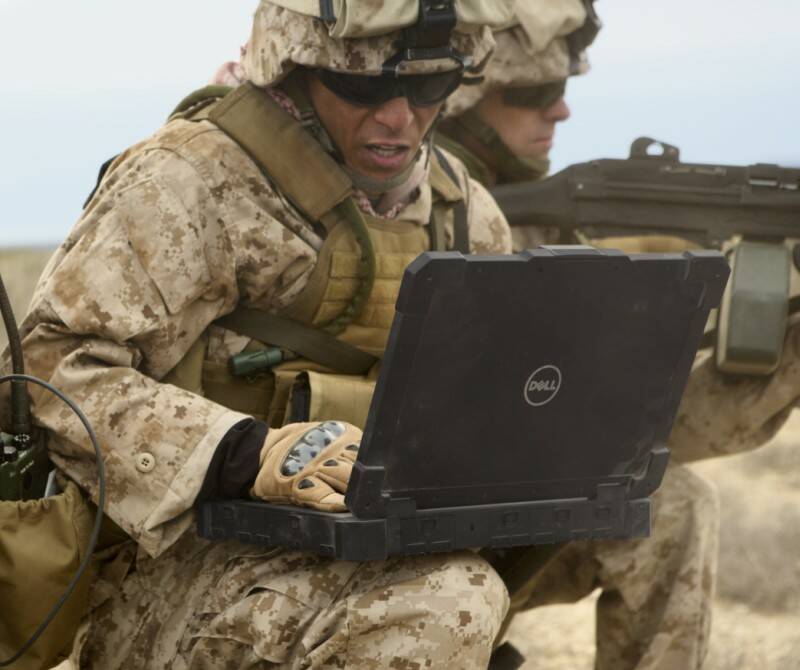
You may not be using your display device under combat conditions in desert heat, but temperature-resilient features of rugged displays may become more desirable as global temperatures increase. (Image © Dell)
Effect of High Temperatures on Electronic Devices
Both heat and cold can cause problems for electronic devices, batteries, and display panels, although the damaging effects of overheating are typically worse. For a desktop computer, the ideal temperature of its operating environment ranges from 10-28°C (approximately 50-82°F), though it should be as close as possible to room temperature, 22°C (72°F). Laptops are typically designed to be operated between 10°C and 35°C (50-95°F). If the operating environment is too hot, then the computer’s internal cooling system, which draws in ambient air, cannot do its job and components may start to overheat.
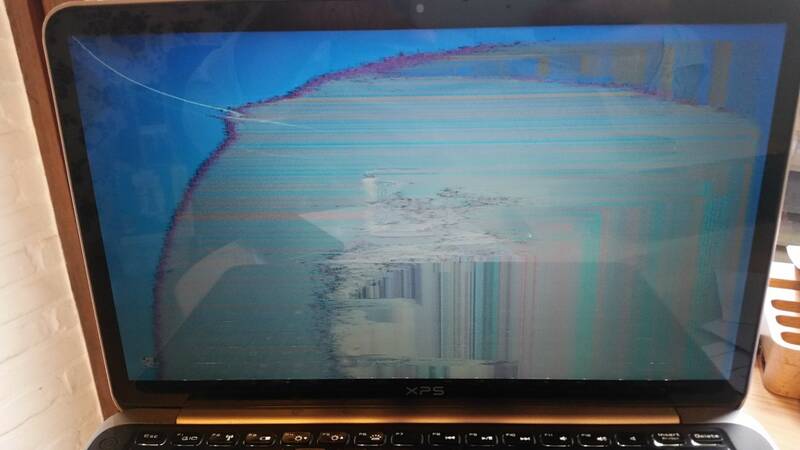
Damage to a laptop screen from overheating. (Image Source)
Most televisions today can safely withstand temperatures up to approximately 51°C (125°F). While LCD screens are generally considered to be more durable than OLED or other newer technologies, if an LCD screen overheats, the liquid crystals inside the panel can deteriorate.
Smartphones are designed to operate normally in ambient conditions up to 35°C (95°F), so it’s not a good idea to leave your phone outside in the sun or in your car on a hot day. Excessive heat can potentially cause damage to the internal electronic components, CPU, adhesives, or even crack the case. Heat can also damage the touchscreen, causing it to malfunction, and cause the battery to drain faster the hotter it gets. Even if your device still operates (after having a chance to cool down), its lifespan is reduced by each overheating event.
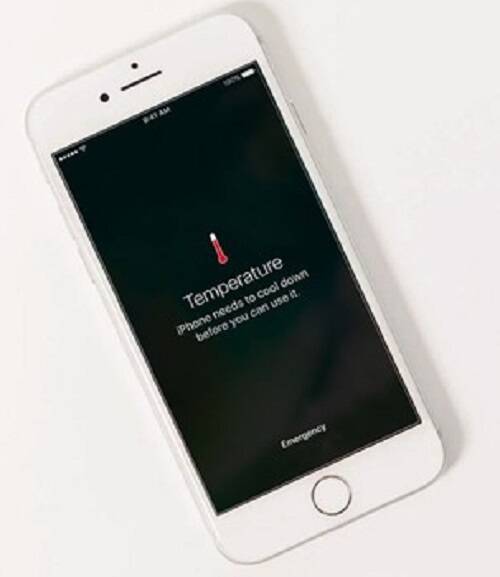
A warning message you don’t want to see. (Image Source: Macworld UK)
New Temperature-Resilient Displays
Research and development in the electronics industry has always paid attention to heat as a design parameter, although historically it was the heat generated by internal components that was of primary concern. But many of the same advances that are helping protect devices can address both internal and environmental overheating, for example, the use of new thermal interface materials. Development of more durable, breakage- and temperature-resistant display components will benefit not only the rugged displays industry but general consumer devices as well. For example:
- Gorilla Glass® from Corning® has been the mainstay for smartphones and other displays since 2005 and has been built into more than 6 billion devices worldwide. It is widely touted for its resistance to scratches and breakage while offering high visual clarity and sensitivity ideal for touchscreens. Manufactured using various processes that include heating to 400° C and an “ion exchange”, Gorilla Glass has similar thermal-resistant properties to Corning’s well-known Pyrex® glass products.
- Sapphire glass is generating excitement for its superior hardness and scratch-resistance, without sacrificing any of the clarity or other qualities of glass cover screens. Sapphire glass also dissipates heat very quickly, which may help mitigate or slow device overheating. Fabricated from aluminum oxide, sapphire screens are technically crystal, not glass, but they can be produced in thin sheets, ground, and polished just like glass.
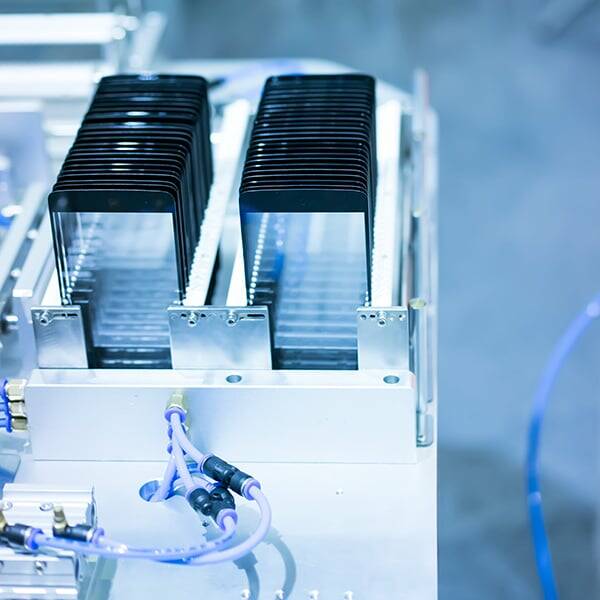
Smartphone display covers in production.
Maintaining Consistent Display Quality In Any Environment
While newer display technologies may provide better durability and resistance to thermal and mechanical damage, visual performance is still key for success across every market sector. Industries that use rugged displays demand consistent legibility and performance, while consumers expect a perfect-looking display out of the box. Manufacturers have long relied on Radiant’s Automated Visual Inspection (AVI) solutions to ensure device quality on the production line.
A solution comprised of a ProMetric® Imaging Colorimeter or Photometer and our TrueTest™ Software enables manufacturers to test display quality and identify defects on today’s high-resolution displays with superior accuracy, efficiency, and completeness. You can tailor pass/fail criteria to address your unique quality concerns, including line and pixel defects, light leakage, non-uniformity, and mura detection. Radiant's systems also excel at assembly verification and surface inspection for non-illuminated components such as glass, plastic, metals, and films used for components from display screens to cases.
To learn more about Radiant’s solutions for automated display testing that ensures high-quality devices from labs to production lines, read the white paper "How to Use Imaging Colorimeters for Automated Visual Inspection of Displays."
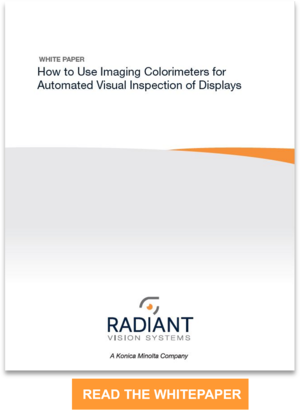
Join Mailing List
Stay up to date on our latest products, blog content, and events.
Join our Mailing List