Breaking the Mold in Automotive: Freeform Displays
With all the places you find digital displays these days, evidence suggests it might not be that hip to be square. Displays that break the mold of the standard rectangular, flat-panel design enable a highly organic integration of display features into shapes and sizes that are a much better fit with their use and environments. Non-rectangular displays are also called freeform displays (sometimes “free form” or “free-form” – pick your poison), denoting their bespoke shapes and alluding to the freedom of design that they offer to device makers.
Freeform displays first gained market attention with the introduction of circular displays. Some notable firsts include wearables like the Android-Wear Moto 360 (first launched in 2014) and Samsung Galaxy Watch (first launched in 2018), and smart home devices like Google’s Nest Thermostat (first launched in 2011), which are much more multi-functional than their analog counterparts. Circular designs are excellent digital substitutes for dials, buttons, and knobs, updating the traditional user experience with improved visual performance, touch controls, and next-gen design that adds a sense of luxury to classic objects.
Android-Wear Moto 360 smart watch (left; Source: Amazon.com), Samsung Galaxy Watch (middle; Source: Samsung.com), and Google Nest Thermostat (right; Source: Google.com).
One market that quickly caught on to the benefits freeform displays offer for organic display integration is the automotive industry. Fresh concepts for automotive design are constantly entering the showroom, yet the general form factor of a passenger vehicle (from its framework to the layout of its interior components) is more or less set. This is due both to roadway safety standards and consumer expectations about where the gear shift, steering wheel, and speedometer are located. Thus, displays that can take on any shape to accommodate a more restrictive layout create opportunities for new display-based automotive systems.
In-vehicle displays have traditionally occupied the center console, relaying digital information for navigation, infotainment, and now-mandatory back-up-camera systems. These rectangular displays have been constrained to the available real estate of the car interior, so as not to overcrowd other necessary components.
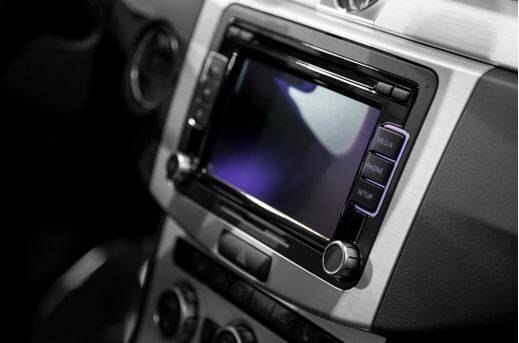
A traditional center-console display used for navigation, infotainment, and rear visibility via back-up camera systems
Rectangles are particularly cumbersome in other areas of the vehicle, like the very space- and shape-restrictive speedometer region. This challenge has contributed to the longevity of analog components in this region of the vehicle, and many new vehicles still utilize analog dashboard designs.
A backlit analog speedometer region (left) and a rectangular display-based speedometer (right).
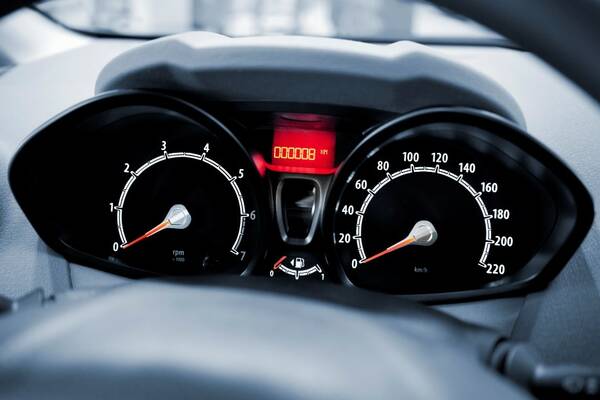
A freeform display-based speedometer offers nearly unlimited freedom in design and new space-saving approaches. At the very least, the freeform display can replicate the shape of traditional speedometer panels.
Automakers looking to swap out analog components in the car interior for digital versions are paying careful attention to how seamlessly a display can occupy the space of traditional interiors. New freeform displays enable designers to maximize the display space within traditional vehicle designs (over rectangular flat panel display integrations) while providing enhanced features and user experience.
Display maker Sharp was one of the first to showcase a number of ground-breaking automotive freeform concepts from its booth at CES 2015, including completely circular, dome-shaped, and bespoke displays. These early designs, applying novel LCD-TFT (IGZO) technology, have inspired many other display makers to imagine how the shape of displays can shape the future of the automotive interior.
Sharp freeform displays at CES 2015. (Source: CNET.com)
Additional images from the Sharp CES 2015 showcase can be seen on Engadget.com.
Technology Enabling Freeform Displays
Predominantly, automotive freeform displays are enabled by LCD (liquid crystal display) technology. If you’re familiar with LCD technology, this may seem counter-intuitive, as there are so many layers that make up an LCD display panel (polarizing filter films, glass substrate, liquid crystal layer, TFT backplane, backlight or reflector). Every layer needs to be cut or shaped in the same freeform pattern to produce a single LCD display.
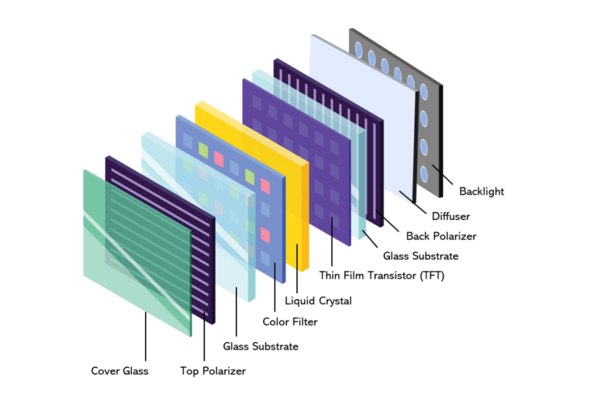
Illustration of layers in an LCD display.
However, the low cost of LCD components and LCD’s long-standing benefits in automotive display integration (durability, longevity, and performance) make a freeform LCD a viable option for many automakers, even with the more elaborate process of cutting and assembly. And, a higher display production cost is likely worth the return from a vehicle featuring the latest freeform panels that will appeal to today’s consumers.
Another challenge with using LCDs is the traditional placement of LCD electronics (namely an LCD’s “gate driver,” which is an integrated circuit that drives current to activate pixels in the display). Sharp addressed this issue in a June 18, 2014, press release regarding its novel freeform display concepts (as shown in the above video):
“Conventional displays are rectangular because they require a minimal width for the bezel in order to accommodate the drive circuit, called the gate driver, around the perimeter of the screen’s display area. With the Free-Form Display, the gate driver’s function is dispersed throughout the pixels on the display area. This allows the bezel to be shrunk considerably, and it gives the freedom to design the LCD to match whatever shape the display area of the screen needs to be.”1
In other words, new technology is enabling the gate driver electronics of the LCD to move from the bezel—which provides a row/column distribution of light-driving power to each pixel along that column or row—to the active display area right behind the pixels, driving power to each pixel much more directly and dynamically. These electronics are integrated with the display’s thin film transistor (TFT) layer in various configurations depending on the intended display shape.
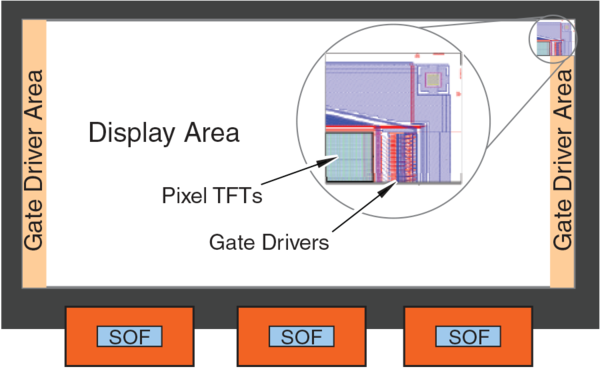
Traditional displays require a rectangular shape and minimum bezel width to accommodate gate drivers on the edge of the display. (Image Source: Sharpsma.com)
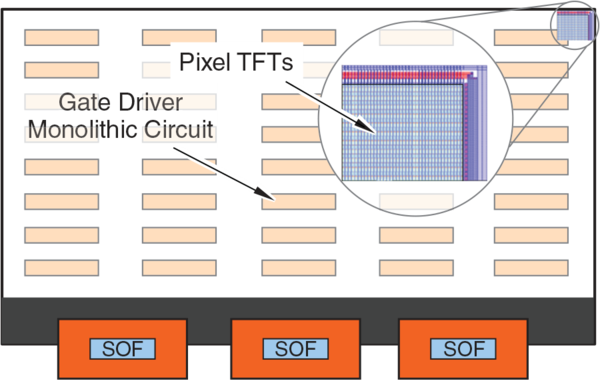
By moving circuitry out of the bezel and into the active area of the display, the bezel is freed from design constraints and the display can be cut into virtually any shape. (Image Source: Sharpsma.com)
What does this mean? With power driven to the display at any point on the display, display makers can cut display layers into any shape without cutting off power to the display. Thus, LCDs remain a solid contender for freeform display design. Designers are freed from traditional rectangular shapes, and can continue to rely on the benefits of LCD displays for automotive integrations: proven processes and materials that ensure display durability, performance, and longevity.
What about OLEDs?
With all of the hype around OLED flexibility, you might assume (and you’d be right) that OLED technology would easily enable the custom shapes of freeform displays. Plus, flexible OLEDs have been on the market just as long as freeform displays (see early flexible OLED devices like the Samsung Galaxy Round and LG G Flex, both released in 2013).
While OLEDs provide the ultimate device flexibility (since, unlike LCDs, they do not require a backlight), the hallmark of a freeform display is really its shape, not its curvature (at least for now, curved and flexible displays remain their own category). For this reason, the flexibility offered by OLED is not strictly required for freeform display design—and in some cases, it is not even preferred.
LG demonstrates the flexibility of its 18-inch OLED panel. (Source: LG Display)
OLED offers a range of advantages in display performance that make it a coveted technology for new automotive designs. These benefits include greater contrast for better visibility in ambient light conditions, higher dynamic range, better brightness consistency, better response times, and fewer display layers as compared to LCDs—reducing some of the defects that are the result of layering such as light leakage on display edges or mura across the display.
Despite its very enticing benefits, however, OLEDs may not be up to the performance requirements of many in-vehicle displays. This is because displays that are most critical to vehicle operation—such as speedometer displays or center console control panels (any primary display-based Human-Machine Interface, or HMI)—are constantly active during vehicle operation. These displays are subject to countless power cycles whenever the vehicle is started or powered down, and must maintain performance with constant use throughout the life of the vehicle. Automotive-grade displays in these installations require durability, environmental stability, and longevity not currently offered by OLED technology.
Industry standards for automotive components (IATF 16949 and AEC-Q100 & AEC-Q200)2 are designed to put a car’s electronics through their paces, and include testing for component durability and longevity based on failure rates in a range of scenarios. For example, regulated environmental durability testing may subject components to temperature cycling at extremes that range from -40° to 125° C. And, because cars last much longer than consumer electronics, manufacturers typically need to ensure component supply and lifetimes to at least five years, extendable to 10 based on vehicle warranties.
Issues preventing widespread OLED adoption in automotive displays continue to be the short lifespan of blue OLEDs (around 14,000 hours3, with typical LCD lifetime between 25-40,000 hours4), screen burn-in issues, material and production costs, and susceptibility to damage from temperature, water, and other environmental elements that a vehicle must endure. In a primary display HMI for a passenger vehicle, these are untenable risks if performance loss affects vehicle operation. In other integrations where displays are not in constant or critical use, the drawbacks of OLED may not prevent their use.
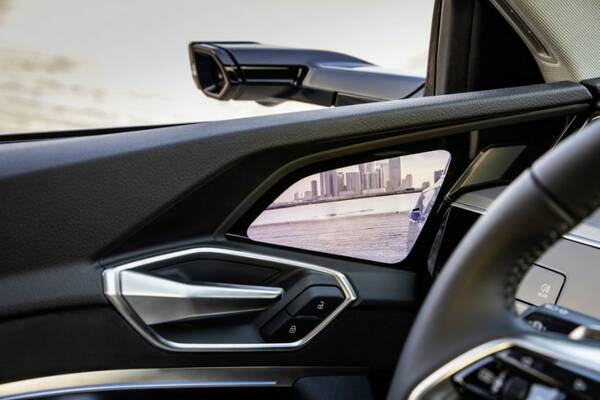
A notable exception: Audi will launch the 2019 e-tron with optional freeform OLED displays by Samsung.5 This displays will take the place of traditional side-view mirrors (in countries where regulations permit it). Has Samsung cracked the OLED-in-automotive code? (Image Source: GreenCarReports.com)
As an example, OLED is certainly fueling the next wave of decorative vehicle lighting. Because of OLED’s flexibility, it can be manufactured in a wealth of shapes and sizes (rows of small OLED panels in taillights to create state-of-the-art designs, OLED light strips along the vehicle interior for brighter ambient colors and color control, and beyond). And, since they are primarily decorative, the performance issues of OLED are not preventative for lighting design. In fact, the benefits of OLED for this type of application far outweigh the costs, offering lightweight, power-efficient systems that can be dynamically controlled to produce extremely unique decorative lighting designs.
OLED concept lighting designed by BMW for the M4. (Source: BMW)
When it comes to displays, while OLED concepts are definitely rampant, we have yet to see many automotive OEMS incorporating OLED technology into production vehicles—and certainly not as the primary display HMI. The technology just isn’t robust enough (yet…?) to enable road-worthy OLED systems. It’s more likely that automakers continue to look toward novel LCD technologies and—as they gain ground—microLED displays to continue to fuel their freeform ambitions.
Ensuring Visual Quality & Performance of Freeform Displays
All displays endure a certain amount of manufacturing and mechanical stress during production and installation. As LCD layers are combined in production, air, particles, and other elements can be introduced between layers, causing non-uniform bonding and visual quality issues that manifest as uneven areas of the display, called mura. Other stresses include bending, pinching, or pressure on a display panel during manufacture or when integrated into an assembly, which can cause similar defects as well as light leakage around the display edges, visible non-uniformity, or dead pixels and lines.
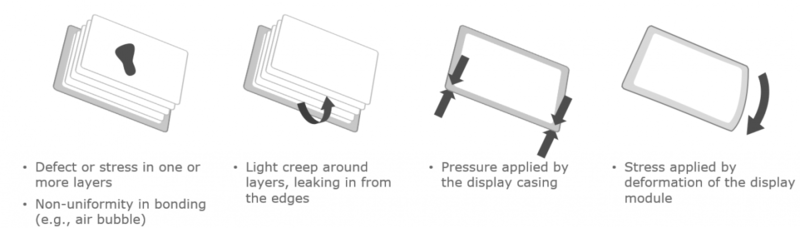
These issues compound as the more demanding methods for freeform display manufacture are applied, such as cutting materials into non-standard shapes and inserting these display modules into non-standard integration spaces. As we’ve discussed, visual performance is a determining factor for a display’s viability for automotive use. When displays perform poorly due to defects, or have low visibility due to uniformity, contrast, and color issues, operability of key display-based HMI in the vehicle can be affected.
The challenge is that traditional display test methods used to measure the visual quality of displays were designed for the characteristics of classic rectangular displays. Especially when it comes to analyzing spatially dependent qualities like contrast, uniformity, and mura (random bright or dark areas across the display), the shape of the display must be taken into account to ensure all areas of the display are measured. Using photometric imaging systems for visual display testing, there has always been a happy match between the rectangular shape of the imaging system’s image sensor and the rectangular shape of the display. Processing the image of a such a display to ensure accurate measurement across the active display area is relatively straightforward – usually a crop and rotation based on the display’s four corners, which align with the row/column layout of pixels in the rectangular image sensor.
Radiant Vision Systems TrueTest™ Software includes a RADA (Register Active Display Area) feature that automatically locates a rectangular display’s corners, and the rotates and crops the image to isolate the active area of the display for accurate measurement.
When it comes to a freeform display, however, isolating the active area of the display is a bit trickier. There aren’t always corners on a freeform display that help to define its shape (or there could be more than four corners!). To address this, Radiant’s TrueTest Software also offers an image processing feature like RADA—but not just for rectangles. It allows the software to ignore any areas of the image visible outside the active display area. This feature is designed to crop out negative area around freeform shapes as well as dark (inactive) areas of a display that are visible beyond a non-rectangular bezel.
This proprietary feature, called RIDA (Register Inside Display Area), locates the would-be corners of a rectangular display area using a test image. The software then zeros-out the inactive area, taking only the active display area into account for measurement. After applying this image processing, the software analyses can determine extremely accurate values for spatially-significant qualities of the display—such as uniformity, contrast, and mura—that require evaluation, all the way to the display’s edges, whether straight or round.
Radiant’s TrueTest Software applies RIDA (Register Inside Display Area) to freeform displays to enable testing on only the active display, regardless of non-rectangular shape.
Radiant’s TrueTest Software and ProMetric® I Imaging Colorimeters were recently demonstrated at the Society for Information Display (SID) Display Week 2019 exhibition in May 2019. At our booth, Radiant showcased a stadium-shape display (also called a “discorectangle”—a fun fact to share at your next social gathering), which was registered in software using RIDA and analyzed for several defects using an automated text sequence.
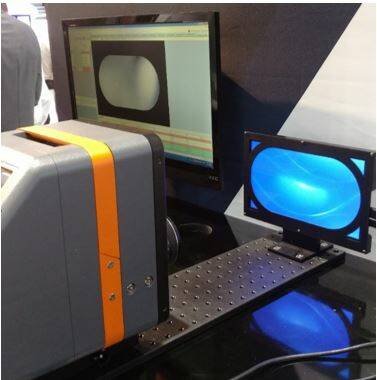
Radiant’s freeform display measurement demo from Display Week 2019, featuring TrueTest Software, a ProMetric I16 (16 megapixel) Imaging Colorimeter, and a stadium-shape display.
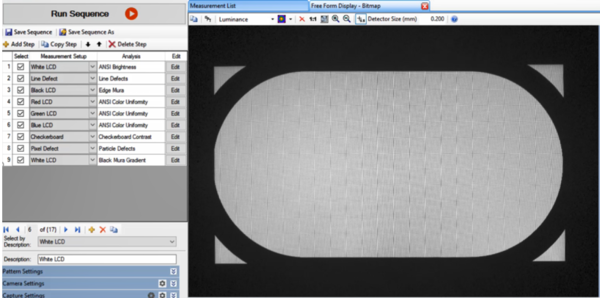
Measurement image shown in TrueTest Software before registration of a stadium-shape display.
After registration of the freeform display (isolating only the central shape of the active display area), analyses can be performed in TrueTest with absolute accuracy. In this example, several tests were applied in succession using an automated test sequence (ANSI Brightness, Line Defects, Edge Mura, ANSI Color Uniformity (RGB), Checkerboard Contrast, Particle Defects, and Black Mura Gradient).
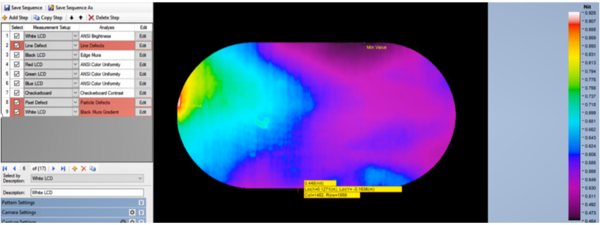
Black Mura Gradient analysis is run on the registration image of the stadium-shape display.
Freeform display measurement features like RIDA—and other important tests for in-vehicle display analysis like Uniformity, Contrast, and Black Mura Gradient analyses—are available in the new TrueTest Software module, TT-AutomotiveDisplay™. This module provides all of the benefits of TrueTest Software to efficiently perform light, color, and mura measurements with specific tests to evaluate unique qualities of displays integrated within vehicles. Learn more about TT-AutomotiveDisplay in the product Specification Sheet:
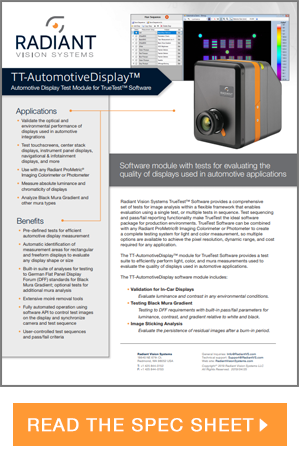
The Next Phase of Automotive Displays
What happens when freeform displays are taken to the next level? Novel shapes meet curved components to produce displays of virtually any shape in all three dimensions. Flexible and curved displays allow automakers to completely renew the 3D architecture of the automotive interior and rethink the role of the display as adaptive to any surface in the vehicle.
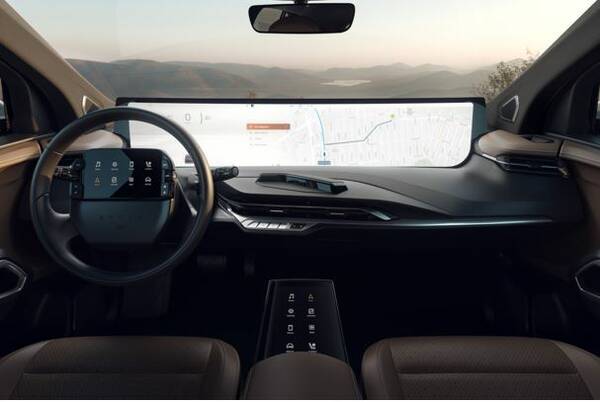
Byton’s concept car premiered at CES 2019 with a 49-inch freeform display screen that spans the width of the windshield. The design also features curved touch displays in the steering wheel and a freeform center console display. (Source: The Verge)
While definitely also very free in their form, curved displays occupy their own category much like flexible and foldable displays. As their own category, they also deserve their own blog, so I’ll save my thoughts on curved displays for a later date.
If you’re interest is piqued, however, be sure to check out the Technical Program at this year’s Vehicle Displays Detroit Symposium & Expo, where Radiant Automotive Business Leader Matt Scholz will present considerations for curved display measurement
![]() |
Vehicle Displays Detroit, Session 5.5 “Methods for Measuring Curved Displays: Evaluating Approaches and System Specifications” Wednesday, Sept. 25th | 9:35 A.M. - 9:55 A.M. |
If you’d like to attend the Vehicle Displays exhibits and get a live demo of our freeform display test (featured at Display Week) at table #37, use Radiant’s pass code ndwJXGS to waive the $50 Exhibit Hall Only fee. See you in Motor City!
CITATIONS:
- Sharp. (2014, June 18). Sharp Develops Free-Form Display, Enables Vastly Greater Design Freedom for Displays [Press Release]. Retrieved from http://www.sharp-world.com/corporate/news/140618.html
- Beasley, H. (2018, January 18). Automotive Quality Standards 101: What Qualification Really Gets You [Blog]. Retrieved from https://www.qorvo.com/design-hub/blog/automotive-quality-standards-101-what-qualification-really-gets-you
- Dhoble, S. J., Swart, H., & Kalyani, N. T. (2017). Principles and Applications of Organic Light Emitting Diodes (OLEDs). Cambridge: Elsevier Science & Technology.
- OLED. (n.d.). In Wikipedia. Retrieved August 20, 2019, from https://en.m.wikipedia.org/wiki/OLED
- Samsung Display. (2018, October 2). Samsung’s 7-inch OLED Display Selected for the Audi e-tron ― Audi’s First All-electric Vehicle [Press Release]. Retrieved from https://www.businesswire.com/news/home/20181002006155/en/Samsung%E2%80%99s-7-inch-OLED-Display-Selected-Audi-e-tron
Join Mailing List
Stay up to date on our latest products, blog content, and events.
Join our Mailing List