Lighting the Way to Passenger Safety: Backlit Sign Testing
On a passenger airliner, backlit displays such as exit signs, fasten seatbelt signs, lavatory signs, and other signage are crucial for both comfort and safety. These products must meet strict tolerances for brightness and color—as defined by each aircraft manufacturer—as well as stringent industry regulations.
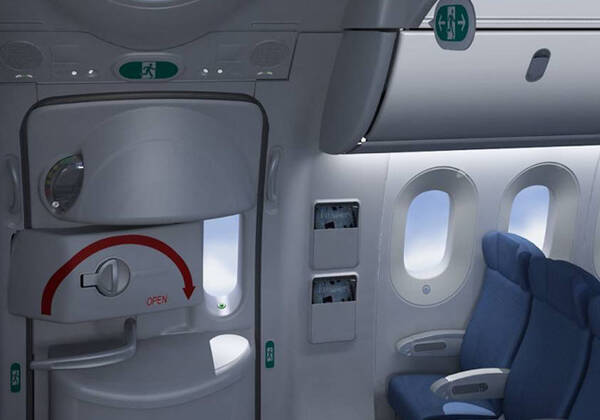
Green exit LED signs light up in an emergency to guide passengers to safety.
Luminator Technology Group is a family of brands that manufacture passenger information signs, lighting, and display solutions for the bus, rail, and aerospace industries. Based in Plano, Texas, Luminator serves a broad customer base in North America and throughout the world. The company’s backlit products include destination signs, passenger advisory boards, infotainment systems, and lighting technology, which enable vehicle operations and contribute to passenger comfort.
The LEDs and colored overlays that are supplied for sign manufacture can vary in consistency from part to part in terms of color value and brightness, making quality control a major focus of Luminator’s operations. Measurement processes at Luminator allow the company to prove its ability meet the various requirements of its end customers and adhere to regulatory standards. The tests that are performed on their signs often evaluate features so minute that they are difficult for humans to perceive.
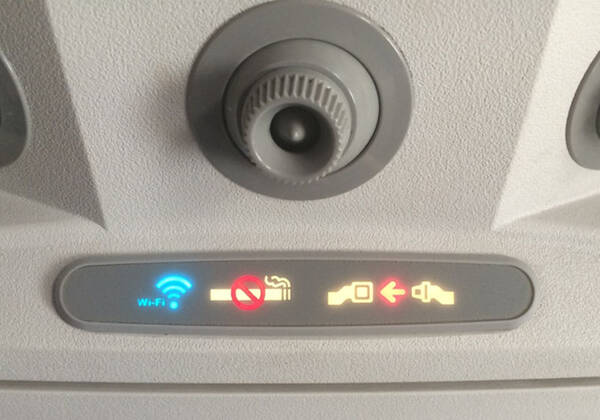
Achieving consistency for all symbols within an illuminated sign—especially where a variety of symbols and colors are present—requires precise digital measurements.
Luminator Aerospace performs extensive light and color measurement tests on each sign that they manufacture. These tests ensure that customer specifications are met to exact values and that a record of verifiable quality data is documented for each part. Measurement criteria vary for each backlit sign, and include strict tolerances for luminance (Lv), color accuracy based on precise CIE color coordinates (Cx, Cy), and other uniformity requirements of light and color and contrast ratios.
In the past, Luminator used spectroradiometers to measure color. Although highly accurate, spectroradiometers are only able to measure a single spot on a component at one time. This makes comprehensive quality testing extremely time-consuming, especially when the process requires an evaluation of luminance and color uniformity across the different illuminated regions of each sign. In these cases, a complete product evaluation could take up to one hour per sign, since the measurement system must be positioned at a variety of points to compare data across the sign.
Luminator needed to find a faster inspection solution. Beyond expectations for product quality, the airplane manufacturing industry has a critical need for on-time delivery. Every day an aircraft is stalled in production due to component delay costs major OEMs millions of dollars in lost revenue.
Luminator selected Radiant’s ProMetric® I Imaging Colorimeters, which can perform a complete product inspection in a fraction of the time. Since implementing with a measurement process using ProMetric, Luminator has reduced its product testing time from more than one hour per sign to as short as three minutes per sign. The ProMetric system can even evaluate multiple signs at once, with as many as eight signs tested in a single measurement, as permitted by the imaging colorimeter’s field of view.
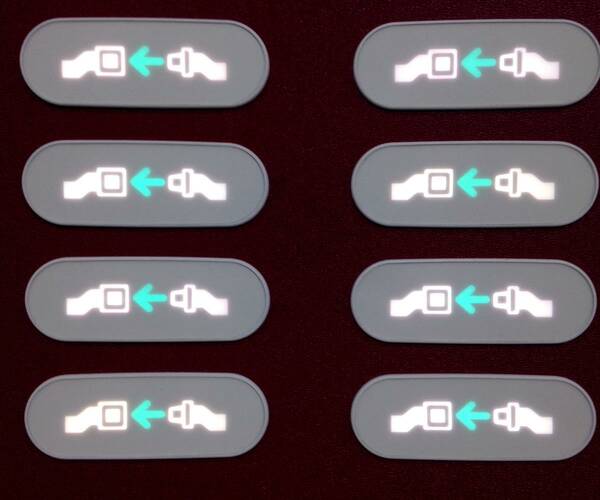
Using a Radiant imaging system, Luminator is able to acquire measurement data for as many as eight signs at once.
If you’d like more details on how Luminator has used colorimeters to improve quality and production efficiency for its backlit signage products, read Radiant’s Luminator Aerospace Case Study to get the full story:
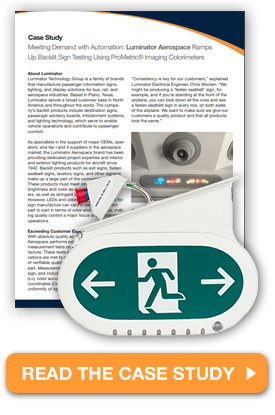
Join Mailing List
Stay up to date on our latest products, blog content, and events.
Join our Mailing List