Quantifying Human Perception in Cosmetic Surface Inspection
Today, customers expect flawless electronic devices right out of the box. Scratched, dented, and otherwise imperfect products can result in damage to your brand reputation and future business. How can you ensure consistent visual quality, i.e., the cosmetic appearance, of delivered products?
Cosmetic surface quality describes defects that can be seen by humans, most importantly product purchasers and users, on the surface of a device such as a smartphone, tablet, or laptops. “Specifically, it defines state of polish, freedom from scratches and digs, and edge treatment of components.”1 To ensure the quality of these and other electronic consumer devices, most manufacturers rely on human inspectors. A key benefit of human quality inspectors is that they are human: they are therefore capable of spotting and evaluating visible defects on a device that will be visible to (human) customer users. A downside of human quality inspectors is that they are often subjective and inconsistent, through the course of a day and from inspector to inspector. In addition, they are typically slower than automated inspection systems for the same detail of inspection.
Automating Cosmetic Surface Inspection
While addressing fatigue issues associated with human visual inspectors, traditional machine vision systems have not typically been able to match their visual acuity when it comes to spotting subtle defects that would mar the customer experience. By using photometry-based methods, Radiant has developed photometry-based surface inspection solutions that can exceed the precision of human inspectors.
Additionally, one weakness of traditional machine vision inspection systems is that they are not effective at spotting random or unexpected defects, or defects that occur in unexpected locations. A photometry-based imaging approach combines camera systems and software to "perceive" surface cosmetic defects the way that humans do, first by capturing images with resolution and dynamic range that match human visual capabilities, and then by applying specialized algorithms that mirror human perception. This visual acuity enables photometry-based systems to capture and assess a full image of a DUT to identify even random defects and areas of non-uniformity.
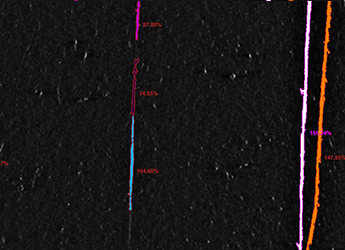
Radiant's photometry-based imaging systems capture and take precise measurements of surface imperfections such as a scratch on a laptop case.
More recently, "deep learning" artificial intelligence approaches have been combined with machine vision systems to improve the capability of these systems to adapt and learn new defect types. However, machine vision systems are still often limited by the quality of images and the level of find detail they can detect. With the quality of photometric images provided by Radiant camera systems, these same AI extensions are also available, with better effect.
The Radiant solution—part of our Advanced Vision product group—offers high-resolution imaging, precision, and the ability to detect and assess subtle and random defects, at production line speed. Advanced Vision combines the accuracy and discernment of human vision with the automation, repeatability, and data capture advantages of machine vision systems, yielding a powerful inspection solution to help ensure product quality.
Photometric Defect Detection
Photometric systems were originally designed for light and color measurement. They are often used today for measuring both illumination from lighting fixtures (such as LEDs and automotive headlamps) and the displays of today’s consumer electronic devices to assess visual performance. These same imaging photometers can be used to inspect illuminated surfaces to detect both physical and visual defects. For example, they can be used to perform:
- Contrast detection
- Spatial measurement
- Non-uniformity detection
- Pattern matching
- Optical character recognition (OCR)
Surface Inspection Lighting
One challenge of doing surface inspection is that the surface itself doesn’t emit light, thus proper lighting for the task is critical for accurate defect detection. There are many lighting options, depending on the type of inspection needed, for example, low angle image lighting is best for detecting cracks in a surface, and structured lighting helps detect fine defects on curved surfaces. If the material is transparent (such as glass) backlighting may also be a component of an inspection setup. Determining the correct lighting for an application can be quite challenging. Factors Radiant includes when designing the set up for a specific application include a combination of the imaging technology, performance requirements (e.g., line speed), DUT surface material(s), DUT geometry, and more. That said, the diagram below is intended to indicate the breadth of techniques that are considered when optimizing the lighting configuration.
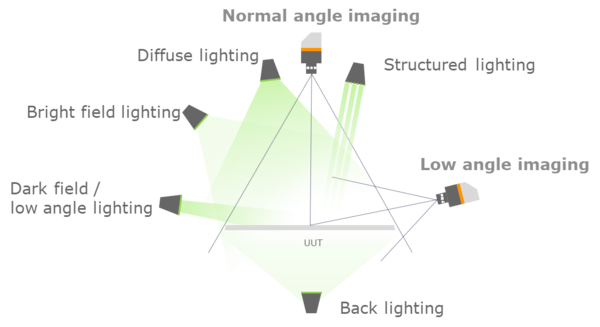
Different types of lighting are needed for various cosmetic surface inspection tasks, depending on the unit under test (UUT).
Cosmetic Surface Inspection Applications
Photometry-based inspection is effective for detecting multiple classes of defects including surface damage (dings, dents, and scratches), surface debris (particles, fibers, and foreign materials), and surface features such as finish (uniformity), fit, and text/logos/labels. Ideally for efficiency and speed, you want to be able to use the same set of images for multiple types of detection. Photometry-based systems can inspect both glossy surfaces (such as display glass, or the instrument cluster in a car), as well as metallic and plastic surfaces with a matte finish.
From an analysis perspective, lighting and measurement conditions can be set up to detect both smudges and particles that rest on a surface as well as scratches and dings that represent changes in surface integrity. Because photometric systems are specifically designed to replicate human vision, they correlate with what a human (i.e., user) would see for a broad range of surfaces and finishes. For example, inspecting a tablet incorporates the surface of the display and the surface of the device housing. Defects can be detected in any of the following elements:
Logo & Text Defects
| Display Area Defects
|
Fit & Feature Defects
| Housing Defects
|
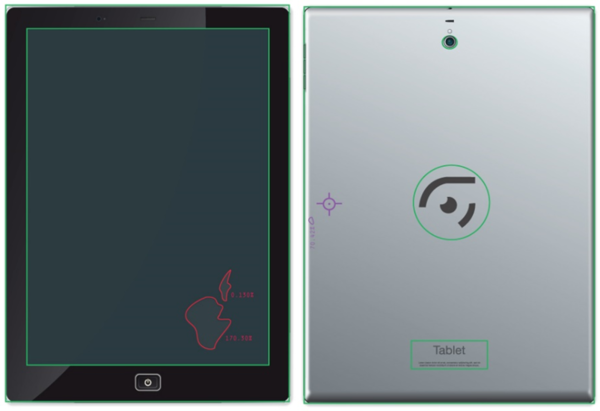
Example of tablet inspection, including glossy display surface and metallic casing, along with component and yrxy elements.
The power of Radiant’s Advanced Vision photometry-based imaging systems is that a single set of images can be used to detect multiple elements at once, including all surface and fit and finish attributes. To learn more, read the Tech Note, “Quantifying Human Vision: Using Photometry-based Imaging Systems for Cosmetic Surface Inspection” or visit our webpages on Surface Inspection and Particle Inspection.
CITATIONS
1. “Cosmetic Surface Quality – U.S. Military Specifications”, from Optical Specifications, Melles Griot
Join Mailing List
Stay up to date on our latest products, blog content, and events.
Join our Mailing List