Seeing Red: Advancements in Red LEDs Bring MicroLED Displays Closer
There has been excitement in the display industry about microLEDs for several years and a few high-end microLED products (such as Samsung’s The Wall) have reached the market. MicroLEDs hold the promise of visually stunning displays with low power consumption, high resolution, quick response rates, and high luminance. They can also incorporate embedded sensors for added device functionality. But production challenges have slowed the emergence of this technology.
Fabricating a microLED display involves many technologies and processes such as epitaxy, photolithography, chip fabrication, substrate removal, inspection, mass transfer, bonding and interconnection, testing, repair, backplane and drive IC, and more. Manufacturers continue to try various methods to increase consistency, raise, yields, and scale up output.
Researchers and developers have long been grappling with issues even at the initial stage of epitaxial crystal growth. The selection of materials and/or methods used to build individual microLEDs can have a significant impact on down-stream display efficiency, color quality, and integration. This post takes a look at some microLED materials challenges—and some new potential solutions.
Making MicroLEDs in Full Color
Just like LEDs, MicroLEDs can be monochrome (configured with only one color) or configured with the three primary colors—red, green, and blue. One-way white LEDs/microLEDs are made by mixing light from the three primary colors to mimic the spectral power distribution of white light. This method is fairly hardware-intensive, however, requiring three LEDs to produce a single white light source.1 Another method of making white LEDs uses phosphor compounds to convert light—for example a single blue LED coated with yellow phosphor will emit white light. Phosphor-derived white light provides better color accuracy and is more energy efficient.2
What determines the red, green, or blue color of an LED is the material that’s used for its semiconductor element. Typically, red, orange, and yellow LEDs in lighting systems are composed of aluminum gallium indium phosphide alloys (AlGaInP, sometimes rearranged as AlInGaP and pronounced “alan-gap”). Indium gallium nitride alloys (InGaN, pronounced “in-gan”) is used for green, blue and white LEDs. (Learn more about the chemistry of color.)
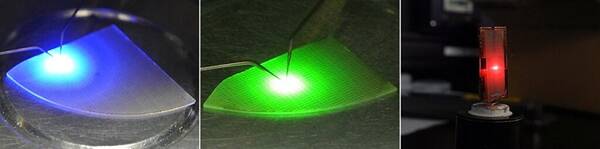
To improve display technologies, engineers must integrate the three primary color LEDs, blue, green and red, onto one chip. (Image Credit: © 2020 KAUST)
But creating the full, vivid spectrum of colors for a microLED display requires that each LED element integrate all three primary colors—red, green, and blue (RGB)—onto one chip. Each colored “chiplet” is one sub-pixel. Fabricating RGB microLED chips has typically been “achieved by mixing nitride LEDs and phosphide LEDs. This mixing causes blue, green, and red LEDs to behave differently in terms of temperature and aging, which impacts image color quality. Moreover, blue, green, and red LEDs each require specific electronic drivers, making integration more complex.”3
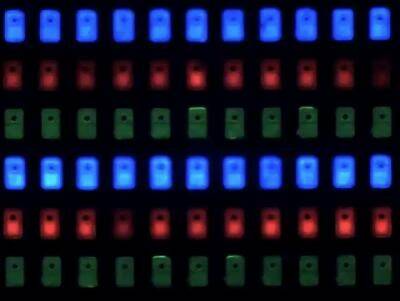
Example of a microLED subpixel array from PlayNitride (Image Source)
The challenge for microLED makers is to find an LED composition material that can span the full color spectrum from blue to red with consistent behaviors and driving conditions. “Theoretically, the indium-gallium-nitride (InGaN) alloy can cover the entire visible range by adjusting the indium content to fine tune the peak emission wavelength. Unfortunately, high indium content in GaN-based LEDs results in poor quality because of lattice mismatches between the GaN buffer layers and the InGaN quantum wells.”4
In the last few years, researchers have been hard at work to find materials that will improve LED consistency and efficiency accross all colors. “The best candidates for generating all three colors are a family of compounds called nitride semiconductors. These are crystals containing nitrogen that in theory can be used to create LEDs that produce light with wavelengths between ultraviolet and infrared, which includes the entire visible spectrum. Engineers usually use gallium nitride to make blue and green LEDs, but they have struggled to make bright red LEDs with this crystal.”5
In Pursuit of a Better Red LED
Recent developments in producing red LEDs may help address these microLED color challenges. In 2017, researchers at Soitec developed an innovative substrate called indium-gallium-nitride-on-X, or InGaNOX (InGaN-on-X), that overcomes lattice mismatch and can be used as a seed layer for full InGaN LED growth. “The substrates are suitable for producing high-efficiency green LEDs with direct emission, eliminating the need for phosphor converters”6 and eliminating nitride/phosphide LED mixing.
Additionally, this new InGaNOX technology “could be used to create substrates with mixed lattice parameters, enabling growth of different colored LEDs on the same substrate. This could drastically reduce the cost of microLED mass transfer for microdisplay fabrication.”7
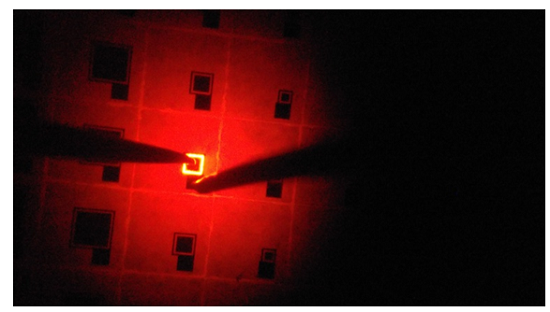
Red emission at 630nm of 100µmx100µm of full InGaN LED grown on Soitec’s InGaNOS (Image: Soitec)
In 2018, a group of researchers from several leading Taiwanese institutions developed a prototype red-light micro LED display made of an AlInGaP epilayer, bonded to a double-polished sapphire substrate. A key process they used to fabricate this LED panel was planarization. A “polymermaterial was used to fill the gap between each pixel, which was used to prevent a short or open circuit using the planarization process.” The display is driven by passive multi-electrode addressable controlling, producing luminance of “more than 450 nits with an operating voltage of 3 V, which is three times higher than that of the OLED operating in the same driving mode.”8
Yet still this wasn’t a universal solution, especially not for displays intended for augmented reality (AR) use, one of the key applications of microLED technology. “While indium gallium nitride (InGaN)-based blue and green LEDs are commercially available, red LEDs are typically based on aluminum indium gallium phosphide (AlInGaP) material or color-converted red LEDs. For augmented-reality applications, achieving high-efficiency ultra-fine-pitch red pixels (<5 µm in size) remains elusive due to severe edge effects from AlInGaP material and cavity losses from color-conversion processes.”9
Then in December, 2019, Plessy announced the successful development of an efficient InGaN red LED with the “capability to manufacture native blue, green and red InGaN material or tune wavelengths from 400 – 650 nm using its GaN on Silicon platform.” InGaN-based red can potentially lower manufacturing costs, is scalable to larger 200 mm or 300 mm wafers, and has a better hot/cold factor than AlInGaP-based red. Plessy developed “a proprietary strain engineered active region to create an efficient InGaN Red LED.10
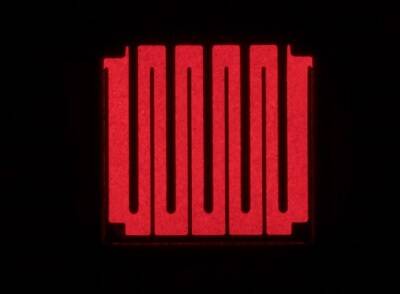
A Plessy native-red LED on Si (Image © Plessy)
Then just last week, a team at KAUST announced that they had achieved the elusive goal of making pure red LEDs from nitride crystals. In their May 7 announcement, group leader Kazuhiro Ohkawa explained: "Red vision has been almost impossible—other groups have only really succeeded in making orange, not apple red. Now, we have developed a crystal growth system to realize pure red LEDs."11
Replacing some of the gallium in an LED crystal with indium should theoretically yield the desired red color, but thus far this has been challenging because indium easily evaporates. The KAUST team “created a reactor with extra indium vapor above the crystal's surface, a process known as metalorganic vapor-phase deposition. This added pressure prevents the indium in the crystal from escaping.”12 The team also added some aluminum, whose small molecules help to reduce crystal defects. The resulting LED has been shown to operate at about half the voltage of previous red LEDs.
It's Not Easy Being Green
Green LEDs have not been without their challenges also, particularly in terms of energy efficiency. Today most green InGaN microLEDs are produced by combining a standard photolithography technique with subsequent dry-etching processes on a standard III-nitride (AlN, GaN, InN) LED wafer. In January, researchers from the University of Sheffield announced a new fabrication method for green InGaN microLEDs that avoids the dry-etching processes, which can damage the surface of the crystals. These efforts are being continued by spin-off company EpiPix, Ltd.
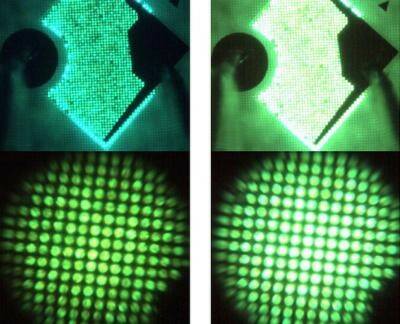
Green, 3.6 μm micro-LEDs that could be brightly lit at an ultra-low driving current of 0.3 μA under a 2.5V bias. (Image Source)
All of these recent developments have moved microLEDs closer to realizing their full potential of bright, energy-efficient, colorful displays for consumer devices. R&D has been helped along by laboratory testing and measurement, and quality inspection will then be needed as microLED displays move into factory production.
MicroLED Color Qualification
Throughout the process of producing microLEDs—from epitaxy to final device assembly—the need for quality control is paramount for increasing yields and achieving the commercial viability of microLED devices for consumer markets. Accurate measurement of color, luminance, and uniformity needs to be performed at the chip/wafer level and at the panel/assembly level.
For extremely precise inspection of individual pixels and subpixels, Radiant’s ProMetric® Imaging Colorimeters—when used alone or with the add-on Microscope Lens—capture and measure every display pixel with precision, regardless of subpixel layout. Our systems can capture an image of an entire display to identify areas of non-uniformity and blemishes (mura), but with sufficient resolution to also examine every pixel in detail.
The Radiant Microscope Lens enables the resolution of our imaging systems to be applied to a very small (zoomed-in) portion of a display or wafer, for exponentially greater measurement precision at each light-emitting element (each individual microLED/subpixel). These comprehensive measurements enable very efficient pixel uniformity testing and calculation of correction factors for display calibration.
To learn more, read our white paper: “How to Use Imaging Colorimeters to Correct OLED, MicroLED, and other Emissive Displays for Improved Production Efficiency and Yields”. In it we discuss how imaging colorimeters can be applied to improve OLED and microLED display production by measuring brightness and color uniformity at the pixel and subpixel level, and we explain the “demura” process to correct poorly performing subpixels to ensure quality displays and safeguard your manufacturing investment.
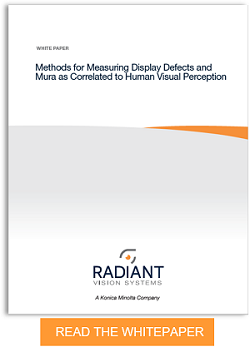
CITATIONS
- “How LEDs produce white light”, PhotonStar Technology, LTD. (Retrieved May 14, 2020)
- Ibid.
- Evangeline, H., “Disruptive substrate technology for direct green and red micro LEDs” LEDinside, October 17, 2017
- Ibid.
- King Abdulla University of Science and Technology (KAUST), “Pure red LEDs fulfill a primary goal”, Phys.org, May 7, 2020
- Evangeline, H., “Disruptive substrate technology for direct green and red micro LEDs” LEDinside, October 17, 2017
- YiningChen, “Soitec’s Relaxed InGaN Substrates Enable Pure Red Emission for Full-Color Micro LED Displays”, LEDinside, November 5, 2018
- Horng, R., et al., “Fabrication and Study on Red Light Micro-LED Displays”, Journal of the Electron Devices Society, Vol. 6, August, 2010. DOI: 10.1109/JEDS.2018.2864543
- “Plessey develops native red InGAN LEDs on silicon for micro-LED displays”, Semiconductor Today, December 6, 2019
- “Plessey delivers native Red InGaN LEDS on Silicon for world leading microLED display”, Plessey Press Release, December 5, 2019.
- King Abdulla University of Science and Technology (KAUST), “Pure red LEDs fulfill a primary goal”, Phys.org, May 7, 2020
- Ibid.
Join Mailing List
Stay up to date on our latest products, blog content, and events.
Join our Mailing List